Das Teil befindet sich in einem geheimen, unterirdischen Raum auf dem Schaeffler-Gelände in Schweinfurt. Bewacht von Soldaten, geschützt hinter Panzerglas. Sonores Summen, pulsierend wechseln die Farben. Grün, rot, blau. Hellweiße Lichtblitze.
Nichts dergleichen. Ganz unspektakulär liegt da ein ringförmiges Objekt auf einem kleinen Tisch. Daneben andere, ähnliche Werkteile aus der Schaeffler-Produktion: Hubschrauberlager, Getriebelager, Hauptwellenlager, Raumfahrtlager. Damit fliegen also Raumschiffe ins All?
"Ja", sagt Peter Glöckner, Leiter Forschung und Entwicklung bei Schaeffler Aerospace Schweinfurt. Das etwa zehn Zentimeter durchmessende Wälzlager in seiner Hand war ab 1995 fast zwei Jahrzehnte lang ein Bauteil im Space Shuttle, jenem Raumfähren-Programm der amerikanischen Raumfahrtbehörde Nasa, das von 1981 bis 2011 lief. Noch heute wird das Teil unter anderem in der Ariane-5-Trägerrakete der europäischen Raumfahrtbehörde Esa verbaut. Es schaut unspektakulär aus, hat es aber in sich.
Schweinfurt erschließt sich Luft- und Raumfahrtsektor
Eingestiegen in das Luft- und Raumfahrtgeschäft ist Schweinfurt vor genau 50 Jahren, es war die Zeit der ersten bemannten Mondlandung: Am 20. Juli 1969 betrat Neil Armstrong als erster Mensch den Mond. Um 21:54 Uhr (amerikanische Zeit im Missionskontrollzentrum Houston, Texas) setzte der damals 38-jährige Astronaut und Kommandant der Apollo-11-Mission seinen linken Fuß auf die Oberfläche des Erdtrabanten und sprach die berühmten Worte "Das ist ein kleiner Schritt für einen Menschen, aber ein großer Sprung für die Menschheit." Kurz danach stieg auch Buzz Aldrin aus der Landefähre Eagle (Adler) aus, Michael Collins als Pilot der Kommandokapsel umkreiste derweil den Mond und wartete auf die Rückkehr seiner beiden Crew-Mitglieder. Am Ende ging alles gut, der Rest ist Geschichte.
In Schweinfurt ereignete sich nahezu zeitgleich Folgendes: Der "Erzeugnisbereich Fluglager" bei FAG Kugelfischer wurde gegründet. Die Idee: das Geschäftsfeld Luft- und Raumfahrt erschließen. Das ganze mündete darin, dass die FAG Aerospace heuer 50-jähriges Bestehen feiert und seit April 2019 unter dem Namen Schaeffler Aerospace Germany GmbH firmiert. Schaeffler hat die FAG Kugelfischer Schweinfurt im Jahr 2001 übernommen und die Sparte Luft- und Raumfahrt weiter ausgebaut, wie Christian Bald erklärt, Unternehmenssprecher für Industrie und Maschinenbau.
Der Betrieb vergrößert sich
Hatte der "Erzeugnisbereich Fluglager" zunächst nur rund 20 Mitarbeiter und eine halbe Millionen Euro Umsatz gemacht (1972), ging es mit der Spezial-Wälzlagerfertigung aus Schweinfurt im Laufe der Jahre stetig bergauf: 1981 machte das Werk zehn Millionen Euro Umsatz, im Jahr 1987 waren es 25 Millionen Euro. 2006 lag der Umsatz nach Unternehmensangaben erstmals bei über 100 Millionen Euro. Im Industriekonzern Schaeffler (Umsatz 2018: rund 14,2 Milliarden Euro, weltweit rund 86 000 Mitarbeiter) ist die Aerospace-Sparte mit 550 Mitarbeitern ein kleiner Betrieb.
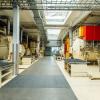
Aber ein wichtiger Bestandteil im Gesamtgefüge der Schaeffler-Gruppe. Wie Peter Glöckner erklärt, leistet die Aerospace-Gesellschaft viel Pionierarbeit. Hier werden neue Werkstoffe entwickelt, neue Verfahren ausprobiert, technische Maßstäbe gesetzt. Hinzu kommt, dass alle Schaeffler-Gesellschaften innerhalb des Konzerns gut vernetzt sind, wie Armin Necker erläutert. Wissen und Erfahrung aus verschiedenen Geschäftsfeldern kämen so zusammen und würden ausgetauscht. Necker ist der Geschäftsführer des Standorts Schweinfurt bei Schaeffler Aeorospace.
Wälzlager aus Schweinfurt: "Präzision ist das A und O"
Im Hauptgeschäft werden am Standort Schweinfurt Wälzlager für Flugtriebwerke hergestellt. Kunden wie Rolls-Royce oder Pratt & Whitney setzen auf die Technik und das Know-how aus Schweinfurt. In der Luftfahrt ist höchste Qualität gefordert, jedes Bauteil unterliegt strengsten Sicherheits- und Prüfkriterien, für Ungenauigkeit ist hier kein Platz. "Triebwerke müssen absolut zuverlässig arbeiten. Präzision ist das A und O", sagt Necker. Er zeigt auf dem Werksgelände in Schweinfurt das Teil-Modell eines Trent 900 Triebwerks von Rolls-Royce. Das Triebwerk wird im Airbus A380 (größtes in Serie produzierte Flugzeug der zivilen Luftfahrt) eingebaut und leistet bis zu 50 Megawatt pro Turbine (rund 68 000 PS).
Erfahren und gut vernetzt
Diese Kraft übertragen die Wälzlager aus Schweinfurt auf das Flugzeug, damit der in den Brennkammern erzeugte Schub für die nötigen Flugzeugbewegungen genutzt werden kann. Es ist ein hochkomplexes Zusammenspiel verschiedener Bauteile, jeder noch so kleine Fehler im Gesamtgefüge könnte zu immensem Schaden führen.
Diese Verantwortung tragen die Schaeffler-Mitarbeiter allerdings nicht mit Bangen, sondern mit Stolz, wie Necker verdeutlicht, denn sie wüssten um ihre Fähigkeiten. "Das ist unser großer Vorteil: Wir haben sehr viele erfahrene Mitarbeiter, die viele Jahre im Unternehmen sind." Sie kennen Abläufe, Zusammenhänge und haben viel Fachwissen, das bei der Produktentwicklung, Forschung und Produktion einfließt. "Das macht uns so schnell keiner nach."
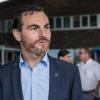
Darauf bauen auch die Flugzeughersteller und Fluggesellschaften. Wer also bald mal wieder im Flugzeug sitzt und aus dem Fenster auf die Turbinen schaut, kann sich sicher sein, dass darin ein Schaeffler-Wälzlager eingebaut ist. "In jedem Flugzeug sind wir dabei", sagt Ingenieur Peter Glöckner. "Und in jedem Hubschrauber."
Der 39-jährige Ingenieur arbeitet seit 15 Jahren bei Schaeffler Aerospace und weiß um jedes Schräublein in diesem Betrieb. Jeden Mitarbeiter, der ihm über den Weg läuft, grüßt er freundlich und nennt ihn beim Namen. Zuständig ist er unter anderem für Forschung- und Grundlagenentwicklung.
Standort Schweinfurt: 30 000 bis 50 000 Wälzlager für Luft- und Raumfahrt
Im Aeorospace Werk in Schweinfurt werden laut Glöckner zwischen 30 000 und 50 000 Wälzlager pro Jahr gefertigt. Davon sind nur etwa 500 bis 1000 für die Raumfahrt bestimmt. Klar, das sei ein Nischenprodukt, sagt Glöckner. Aber die zunächst kostspielige Forschung aus dem Raumfahrtlabor zahle sich aus: Wenn zum Beispiel Werkstoffe, die für die Raumfahrt entwickelt wurden, auch in die industrielle Serien-Fertigung gehen, weil sie dort ebenfalls gebraucht werden. So etwa geschehen bei dem Werkstoff "Cronidur 30", den FAG vor fast 30 Jahren als gemeinsames Forschungsprojekt mit der VSG Energie- und Schmiedetechnik Essen und der Universität Bochum auf den Weg gebracht hat.
Dieser Wälzlagerstahl öffnete dem Schweinfurter Unternehmen damals die Tür ins All: 1995 wurden daraus gefertigte Speziallager erstmals in den Turbopumpenantrieb eines Space Shuttles eingebaut, die Raumfähre Atlantis flog damit zur russischen Raumstation Mir, die bis zu ihrer Ausmusterung im Jahr 2001 den Erdorbit umkreiste. Der Werkstoff Cronidur 30 war so erfolgreich, dass er für weitere Raumfahrtprojekte wie etwa die europäische Ariane-5-Rakete verwendet wurde (ebenfalls für die Turbopumpen) und auch in der zivilen Luftfahrt zum Einsatz kommt, so werden etwa auch Hubschrauber damit ausgestattet, erklärt Glöckner.
Cronidur 30: korrosionsbeständig und robust
Was Cronidur 30 so erfolgreich macht, ist seine extreme Korrosionsbeständigkeit und ausgesprochene Robustheit. Glöckner schildert am Beispiel des Space Shuttles, was ein Cronidur-30-Wälzlager leisten muss: Die Turbopumpen versorgen die Haupttriebwerke der Raumfähre mit extrem kalten, flüssigem Wasser- und Sauerstoff, beide Stoffe werden in der Brennkammer zusammengeführt und reagieren dort miteinander. Die vorgeschalteten Pumpen sind dabei Temperaturen von über minus 200 Grad Celsius ausgesetzt.
Die Schaeffler Rollen- und Kugellager in den Pumpen müssen zum einen diese Temperaturen aushalten und noch dazu ohne Schmierung auskommen, da übliche Schmierstoffe wie Öl oder Fett bei diesen Minusgraden ihren Zweck nicht erfüllen. Durch die spezielle Bauweise mit Rollen und Kugeln aus Hochleistungskeramik und einer speziellen Käfigkonstruktion (der Käfig hält die Kugeln und Rollen zwischen den Ringen in gleichmäßigem Abstand) gelang es FAG, einen bis dato nicht gekannten Qualitätsstandard in der Raumfahrttechnologie zu setzen.
Space Shuttle: Mehrere Starts möglich
Werner Trohjan, der damals als FAG-Ingenieur den Werkstoff Cronidur 30 mitentwickelt hat, erinnert sich an den ersten Flug der Atlantis mit der Technik aus Schweinfurt im Jahr 1995: "Da schaut man dann schon mit anderen Augen hin." Nach jeder Mission waren der Nasa damals laut Trohjan Unkosten von rund einer Millionen Dollar für das Auswechseln der Verschleißteile in den Turbopumpen entstanden, was sich mit dem Einsatz des robusten Werkstücks aus Schweinfurt dann änderte: "Mit Cronidur kann man nahezu 100 Starts machen", das sei also ein Sparpotenzial zwischen 90 bis 95 Millionen Dollar für die Nasa gewesen, erklärt Trohjan.
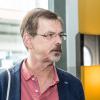
Ganz geht die Rechnung aber nicht auf, wie Franz-Josef Ebert (61), damals Leiter der Produktentwicklung und Vertrieb bei FAG, erklärt: Die Spezial-Wälzlager wurden durch die zuständigen Prüfstellen für jeweils zehn Starts und Landungen freigegeben, dann mussten sie getauscht werden. Freilich hätten sie aber auch mehr ausgehalten, sagt Ebert. In den Tests, die Schaeffler mit den Lagern gemacht hat, war auch nach 50 simulierten Starts noch keine Materialermüdung in Sicht. Cronidur-Miterfinder Trohjan ist überzeugt davon, dass sogar 100 Starts drin sind.
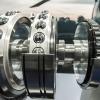
Schweinfurt und die Zukunft der Raumfahrt
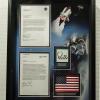
Und wie schaut es mit künftigen Raumfahrt-Projekten bei Schaeffler Aerospace aus, 50 Jahre nach der Firmengründung und der ersten bemannten Mondlandung? Die Nasa und Schaeffler jedenfalls halten weiter Kontakt, sagt Peter Glöckner. Für das Space-Shuttle etwa gibt es Nachfolgeprogramme, so ist Schaeffler-Technologie aus Schweinfurt etwa auch im neuen Raumtransporter Orion (noch in der Testphase) verbaut. Orion ist schließlich auch für weitere bemannte Mondmissionen vorgesehen, Glöckner schätzt, dass das in etwa zehn Jahren soweit sein wird. Schließlich gehe es dann irgendwann auch um eine bemannte Marsmission, aber bis dahin dürften noch mindestens 20 Jahre vergehen. Geplant und gesprochen wird darüber bei den Weltraumbehörden aber freilich schon heute. Und Schaeffler? "Wir sind involviert", sagt Glöckner.
Die Geschichte von Schaeffler Aerospace Schweinfurt1969: Gründung des "Erzeugnisbereichs Fluglager" mit eigenständigem Vertrieb und eigenständiger Entwicklung im Erdgeschoss der Halle H bei FAG Kugelfischer.1972: Erstflug des Airbus A300 im Oktober mit FAG-Kugellagern1975: Beginn der Serienfertigung für das Dreiwellen-Strahltriebwerk RB199 von Rolls-Royce für den Militärjet "Tornado".1976: Ausweitung der Geschäftsbeziehungen zu Triebwerkherstellern wie Garrett (heute Honeywell), Pratt & Whitney, Aerospatiale (heute Airbus Helicotpers) und weitere.1981: Der Fluglagerumsatz im Werk Schweinfurt beträgt rund 10 Millionen Euro1987: Der Fluglagerumsatz in Schweinfurt ist auf rund 25 Millionen Euro gestiegen.1990: Beginn der Entwicklung des Wälzlagerstahls Cronidur 30 1995: Cronidur 30 wird für die Herstellung von Spezial-Wälzlagern für Raketen-Turbopumpen verwendet und erstmals im Space Shuttle für einen Raumflug eingesetzt.2001: FAG Kugelfischer wird von der INA-Holding übernommen (später Schaeffler Gruppe)2005: Gründung der FAG Aerospace GmbH. Im gleichen Jahr erfolgt der Jungfernflug des Airbus A380 mit FAG-Lagern.2006: Umsatz im Werk Schweinfurt erstmals über 100 Millionen Euro. Besuch des NASA-Astronauten Rex J. Walheim im Werk Schweinfurt, der am 8. April 2002 mit dem Space Shuttle Atlantis ins All geflogen war. Das der Hauptantrieb des Shuttles war mit FAG-Lagern bestückt.2009: FAG Aerospace wird als erster und einziger Fluglagerhersteller als luftfahrtbehördlicher Entwicklungsbetrieb zugelassen. Rolls-Royce hat die FAG Aerospace Schweinfurt als Entwicklungspartner für das Trent XWB-Triebwerk des neuen Airbus A350 ausgwählt.2014: Der Raumtransporter Orion fliegt erstmals ins All. In den Turbopumpenantrieb sind Sonderwälzlager der FAG aus Schweinfurt verbaut.2019: Umbenennung der FAG Aerospace zu Schaeffler Aerospace Germany. Großes Mitarbeiterfest zum 50. Jubiläum des Werkes Schweinfurt.Quelle: Unternehmenskommunikation Schaeffler